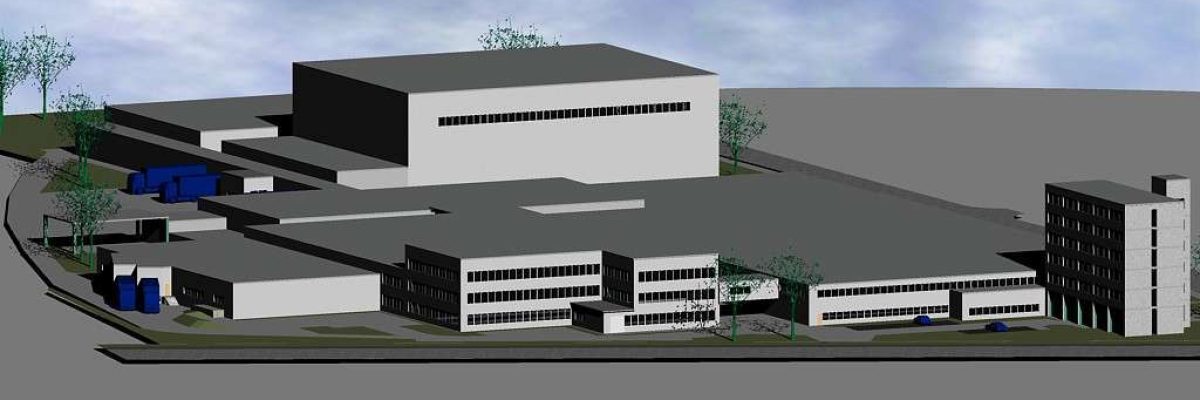
Project task
As part of a factory planning process, HPMlog has developed a logistics concept for gradual implementation, according to which the interaction of production and logistics is optimised in terms of layout and processes. The now centralised inventories are reduced and a continuous flow of materials and information is introduced.
Client
Pharmaceutical manufacturer
Our services
- Record actual material flow and processes
Extrapolate quantity structure according to future growth, taking into account internal projects, e.g. implementation of new machines - Create concept requirements catalog for the areas WE/WA, sample train, central warehouse, connecting corridor and airlocks and identify initial optimization potentials
- Optimize entire factory layout
Reorganization of the area functions, including drug grinding and storage as well as central automatic palletizing - Develop sample train concept (cabin equipment, automation, ventilation / laminar flow and buffers) in connection with the introduction of scanner use in the WE (target processes, documents / labels used, interfaces and hardware)
- Develop airlock concept taking into account the different clean room classes (buffer stocks, repalletising, expansion and automation)
- Dimension central warehouse (warehouse form, automation and on-site requirements GRZ, BMZ)
- Estimate the implementation effort (dates and costs) for the developed logistics concept
Modification requirements during operation and staged concept